Articles and News
The Jewelry Industry Has Jobs, But Some Are Hard To FillSeptember 13, 2017 (0 comments)
|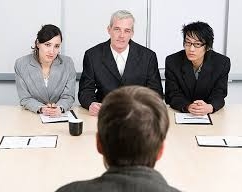
Merrick, NY—No matter which political party is in charge, job creation almost always tops the list of hot button issues. But a surprising number of manufacturing jobs in the United States are going unfilled because of a widening skill gap that prevents workers who need jobs from being hired by the companies that have jobs to fill. No longer simple assembly-line fare, American manufacturing jobs today often require at least some level of technical skill and training. That leaves many workers ill-equipped to step into these roles.
The gap isn’t as prevalent in the jewelry industry, which always has been highly specialized. And because jewelry manufacturing is clustered in certain areas—or passed down in a family—it can be easier for manufacturers to find the skills needed.
Easier? Yes. Easy? Not necessarily.
To quote the famous real estate maxim, it’s all about location, location, location. In jewelry centers, finding skilled workers isn’t a huge challenge, even for companies that require extra-specialized skills. But outside those centers, it’s another story.
“So far, we have not had any problems finding great craftspeople. Sometimes it takes a little more time than in the past, but we have always been able to fill positions,” says Tom Heyman of Oscar Heyman Bros. in New York City. “We do offer full time employment with a good benefit package with health insurance, paid time off, 401K, and others, and I think this makes us a desirable place to work.”
Brian Fleming, president of East Providence, RI-based Carla Corp. also finds no shortage of skilled workers in his area. “Unfortunately, a lot of Rhode Island-based jewelry companies have closed, so that leaves a lot of skilled workers available for us,” he says wryly. Between that and the tight-knit Portugese community in Providence—many of whom are longtime jewelry families—he can hire easily.
But Fleming says Rhode Island in general has an aging workforce, and apart from the Portugese community he doesn’t see a lot of young people, even those without college degrees, getting into the jewelry industry.
“On the creative and designer end there are a lot, but you don’t find a lot of young people who aspire to work a foot press or do stone setting or soldering.” He’s willing to train any high school graduates who do want to work in the less glamorous part of the industry, he says.
Providence, RI has an ample pool of talented jewelry workers. Image: goprovidence.com
Ted Doudak of Riva Precision Manufacturing has brought “every possible jewelry process” in-house to his Brooklyn factory. His motivation was different: Riva specializes in recycled and fair trade gold and he wanted better control of the full manufacturing process.
Speaking at the Initiatives for Art & Culture Gold Conference, he said, “Before manufacturing here in Brooklyn, [manufacturing] was transferring to places like China, India, and Mexico that are not so responsible. That’s left for us to protect, but you have to find bench guys and that’s not easy because we [the industry] sent all our manufacturing away.” He acknowledged there’s more qualified labor available in New York than other parts of the country, but the challenge is that it’s also a very high-cost market and workers need to earn enough to put food on the table even as companies need to keep looking for efficiencies.
“It’s getting tougher and tougher and tougher to find jewelers and skilled labor,” maintains Linus Drogs of Michigan-based Au Enterprises, also speaking at the Gold Conference. “Younger people don’t have an opportunity to be exposed to our trade. Guys in my shop have been making jewelry 30, 40 years, and they’re at the end of their career, but to try and find talented young skilled individuals is tougher and tougher. “A successful operation has to have in-house training staff. You have to create your own people.”
“People aren’t properly trained at the vocational level,” said Stewart Grice of Hoover & Strong, refiners based in Richmond, VA. “There is a lot of pressure in society for young children to go away to a four-year college when what we really need in the jewelry industry are people with community college. I need people I can hire who can hit the ground running but I can't ask a graduate engineer to come to work as a machine operator.” He highlighted a program in his native United Kingdom that combined an apprenticeship or sitting guild program with college courses, and students can learn with their hands and in a classroom on alternate days. But here, there’s nothing like that, he said, and nobody to teach it either.
Jeff Feero, managing partner at New York-based Alex Sepkus, is more concerned about consumer shifts away from fine jewelry, period, than he is about finding people who can make it. “Many customers of all designer lines—not limited to our business but fashion at large—are between 50 and 75 years old. We all expected it to be like Disneyworld with a renewable customer base. But I dare say Disney will suffer the same fate in 10 to 20 years unless they too change the experience to match expectations.”
Changing parameters to match expectations also impacts hiring, says Feero. Finding workers with the right skills is less of a challenge for him than finding workers to work 40 hours without any special considerations, such as child care schedules, holding down a second job, or working on their own line on the side.
Immigration, another political hot-button issue, could ultimately impact the jewelry industry if massive restrictions are implemented. To Grice’s point about a lack of vocational training in the United States, many jewelry companies rely on foreign-born workers for highly specialized skills. For instance, most of Oscar Heyman’s craftsmen weren’t born here, though Tom Heyman says all are either long-time citizens or green card holders, and some have done their training here. Carla’s Fleming points to the Portugese community in East Providence: though many are second- and third-generation Americans, they still retain a strong cultural identity and learn skills passed down in a family. And at Alex Sepkus, about 30% of Feero’s workforce is American born.
A scourge (mostly) missed. The jewelry industry isn’t immune to the drug problems plaguing many American cities and companies, but luckily it’s more exception than rule. Whether manufacturer or retailer, the industry’s traditional need for secure hiring has kept it from becoming a problem, says Jon Parker of DJP Executive Search, an employment recruiting firm in Virginia Beach, VA.
Those companies that have a problem finding qualified employees to pass a drug test again are typically outside the jewelry centers. For instance, Stewart Grice in Richmond, VA, said, “If I ask for a graduate engineer, I get 30 resumes. But if I ask for a machine operator, we get three—and two won’t pass the drug test.”
And Lindsey Rubin, whose family owns Republic Metals in Miami, FL, is happy to teach workers the skills she needs them to have. “Even if someone used to be a waiter before [coming to work at Republic], we'll have an expert or master designer encourage and mentor the new person. The person may have little education or experience, but they become an apprentice and learn the skill. It’s kind of like having a school within your own business.”
If they can pass the drug test first, she added.